News
Field and CPL Updates
2006 Greenland
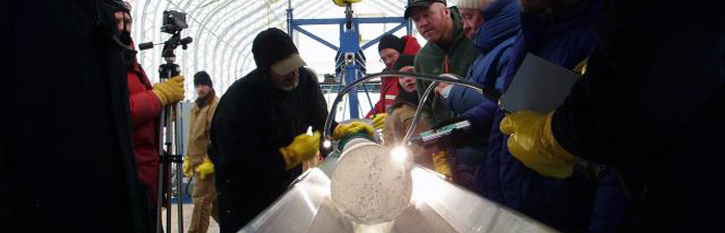
Activity: DISC Drill Test - Summit Greenland
Period: 7/03-7/09/06
Weather Conditions:
Temperature range -28°C to -6°C, wind 0-17 knots
ICDS Personnel on Site:
Jay Johnson
Kristina Dahnert
Michael Jayred
Bill Mason
Nicolai Mortensen
Paul Sendelbach
Scott Hamon
John Fowler
Activities During Period:
Drilling - This week we drilled a total of 58.8 meters. The bore hole depth is 757.5 meters. Average core length was 2.38 meters. The average core length is a little bit shorter than in past weeks because we intentionally drilled several ~2 meter cores. Between the depths of 734.3 and 740.3 three ~2 meter cores were saved by NICL to be used for the brittle ice acceptance test. These three cores will replace the sample cores we drilled last week. Other than the cores that will be drilled during the DV visit, this week marked the end drilling operations for the season.
Scoop Cutter Test - Three more coring runs were done with the scoop cutters this week. Each run was done with different cutter speed/feed combinations. All cores had a ribbed helical pattern on the outside. The pitch of the helix was cutter speed dependent. Aside from the helix pattern the surface of the cores had less surface fractures than cores drilled with the sharp or radiused corner cutters. The helical pattern is most likely being caused by the cutter head wobbling in the bore hole. We have guides on the outside of the cutter head to keep it from wobbling, but I suspect that scoop cutters are either cutting a larger diameter than the guides or the guides aren't large enough. This is just my theory. This next week I will indicate the cutter head to see what diameter the scoop cutters are cutting verses the diameter of the guides.
Modified screen barrel test - Bill was interested to see what effects leaving screens out in the lower portion of the screen barrel would have on the drills ability to collect and store chips. I made a ring that bolted in between screen barrel sections to retain screens in the upper part of the barrel and leave the lower part of the barrel totally open for chip collection. Test runs showed no gains from leaving screens out. In fact core lengths got shorter as more screens were taken out. A second test we did was shortening the core barrel to 3.1 meters and adding two screens to the screen barrel. Cores drilled with this barrel configuration were no longer than ones drilled with two less screens, ~2.7 meters. We saw less of a chip pack on top of the core, but the screens weren't fully packed. With two extra screens we should have been able to drill a full 3 meter core. Have we found the pump's limit? What effect is drilling without the densifier having on chip transportation and packing?
Power monitoring - Correction from last weeks report. Nicolai is using data logging software from Multitek, the manufacture of our power monitor, not Labview. He is generating graphs from the raw data using Mathcad. Data has been logged from several drill runs through out the week.
Update provided by Geoff Hargreaves and Brian Bencivengo NICL
Activity: NICL Greenland Test
Period: 7/03-7/09/06
NICL Personnel on Site: Geogg Hargreaves, Brian Bencivengo
Activities During Period:
7/03/06 Monday
- Brian took DOI internet computer security test. Geoff worked on RPSC 90% drawings, and emails from work.
- Brian made V trays, logged and bagged core and stored in trench.
- We setup shelving for drying booth.
7/04/06 Tuesday
- Brian logging and storing core. Found that we are unable to print core cards. Geoff located the problem, cards print from inventory page which has to be separately filled out (why do we have an inventory page for the field?).
- Also found the DB rounds up core lengths (2m tray file) to 2 places instead of 3.
- ICDS continues to have depth indicator problems, it has been a problem for a while and it's getting worse.
- Touch-off depths are significantly different from previous bottom break depths. They are trying to figure it out.
- Drying booth almost finished, about 85%.
- Brian took 24 hour sample from run #264, and put in sample jar and stored in basement.
- Continued logging and bagging core and storing in the basement.
- Geoff working on drawings to check ability to downsize trench and park ice upstairs at WAIS Divide
- RAN BRITTLE ICE TEST
- ICDS drilled three each ~2m cores.
- Core 1, excellent core w/1 break at ~65.3 cm from top and one spall from FED.
- Core 2, Excellent core, 1 DB 42-75cm, spall at 191cm to 207cm.
- Core 3, very good core, one break at 45-48cm 1 spall from top to 25cm, (720 gm), 1spall 24.5cm terminating at the break at 45cm (515gm) the remaining piece of the top (down to 45cm) was over 2kg.
7/05/06 Wednesday
- ICDS tested scoop cutters, got very interesting helical pattern on core.
- The helix was formed by a several helical ridges, between the ridges was a shallow depression. The ridges showed surface fracturing, the depressions in between were clean, relatively smooth and fracture free.
- Finished drying booth setup after dinner.
7/06/06 Thursday
- Ran extension cords out to trench and fired up the fan.
- Built the last V trays that we can make.
- Tested turkey netting (wine netting?) and it worked very well.
- Core was pushed into the netting after the FED, and Brian smashed up a perfectly good core. Netting contained all but the smallest pieces.
- Geoff worked on emails, and drawings.
- Brian adjusted discharge vents for even flow.
- Collected and logged more core for drying testing.
- Tested an Infrared thermometer, and checked it against the Omega. IFR = -24.5, Omega -24.9. It appears to work, we aren't sure about calibration of either so can't tell which is closer to the truth
7/07/06 Friday
- Tried towel wipe down test again. Previous tries were hard to tell with white blotter paper, we switched to brown paper hand towels, it's easier to see damp/wet from dry.
- After running the ice through FED the blot test showed remaining fluid on core, after thoroughly wiping the ice down with a bar towel, the blot test showed the core was dry. Since the outer surface of the core is quite smooth, it makes it much easier to dry. The bar towel after wiping down, was not very damp (ok, it's cold and hard to tell, but it is not dripping wet and the towel doesn't even seem damp). The towel dries pretty just being set on a counter.
- Brian did soak a bar towel and hang it out to dry.
- Ran another turkey netting test and the netting worked very well.
- Jay turned a round of HDPE to be used as an alignment jig for the ICDS optical alignment system. Brian helped run the alignment test.
- This part will have to be remade when we get the extruded trays.
7/08/06 Saturday
- Geoff, Jay, and Brian poured new liner for FED. (three times, leaked, fell over?)
- Unable to hold temperature conditions required for the material, but we tried it anyway.
- Brian started a drying booth test.
- Checked bar towel drying test, still damp and smells of isopar.
- Checked ice in drying booth after ~5 hrs, blot test shows still some wet patches but mostly dry.
7/09/06 Sunday
- Checked on FED tried to de-mold, not quite cured, put in front of load bank to heat up, hoping to cure the urethane better. Worked on fixing a couple of things. Removed lay flat from AL V tray and installed glue down HDPE. See if it stays stuck to tray.
- Put some of the stick down HDPE under the V tray so it can slide more easily on the receiving table.
- Checked core in drying booth about 30 hrs after starting and blot test shows that the core is dry.
- Played with Geoff's collimator laser alignment tool. Shows promise, but needs to be build from properly machined aluminum parts.
Comments (Problems, Concerns, Recommendations, etc.):
- Casting with soft (A60 durometer) urethane molding compound is a complete failure. We were unable to hold temperature constraints, so the compound failed to cure properly and the mold release didn't release.
- After seeing how soft this molding compound is, I believe that it would not make a good liner, it would most likely snag fractured ice and cause a jam.
- I need to rethink my mold plug in order to extract it out of the liner after casting, but I think that the process holds promise, and will try again with hard smooth urethane when we return to Denver. The hard urethane is much easier to mix and pour, it has no 120F temperature constraints, should be easier to use in the field if necessary.
- The anemometer we brought with us has failed. Air speed will have to be by guestimation.