News
End of Season Field Reports
2012-2013 Field Season
Ice Drilling Design and Operations (IDDO) Activities at WAIS Divide 2012-2013 (T-350)
NSF-OPP supported
PI: Charles Bentley (University of Wisconsin-Madison)
Field Team:
The IDDO field crew consisted of eleven drillers lead by Jay Johnson, IDDO Drill Operations Engineer and Kristina Dahnert, IDDO Field Support Manager. The field crew and the dates of their stays at WAIS Divide are shown in the following table.
Name | Date In | Date Out |
Patrick Cassidy | December 8 | February 1 |
Kristina Dahnert | November 22 | February 1 |
Dave Ferris | December 8 | February 1 |
Chris Gibson | November 30 | January 7 |
Jason Goetz | December 8 | February 1 |
Josh Goetz | November 22 | February 1 |
Mike Jayred | November 30 *
|
February 1 |
Jay Johnson | November 30 | February 1 |
Tanner Kuhl | December 8 | February 1 |
Nicolai Mortensen | November 30 | January 28 |
Elizabeth Morton | November 22 | February 1 |
*Jayred's arrival at WAIS Divide was delayed by accident at McMurdo
Season Overview:
- Camp opened on schedule.
- Weather was a bit worse than the past few seasons - storms each week with blowing snow and poor visibility.
- Warmest day was January 14 with high of -4C (24F).
- Thanks to excellent winter berm building the previous season, camp structures were quickly erected and heavy equipment fully operational quickly despite the secondary carpentry crew's arrival being delayed.
- No lost days due to weather
- Elizabeth, Josh and Krissy of IDDO along with Don Voigt, the SCO Representative, arrived in camp after the end doors of the Arch had been excavated and repairs on the doors started.
- Drill Arch sustained additional damage over the winter
- Floor buckling was substantially more than in previous years
- Floor heaving near slot entrance was severe
- Floor panels were removed in order to remove some of the insulation below
- Footers were fully reworked in certain areas
- Floor near back door had to be recessed so doors would open and cargo could be set inside
- Slot did not have to be excavated for drill tower clearance and slot drip pans were usable in spite of the severe buckling.
- Optical table had to be re-leveled.
- Cargo Movement
- All cargo arrived at WAIS quickly
- Carrie Schaffner, new WAIS Divide Cargo Coordinator, did a great job.
- Tony Wendricks and Eric Thompson in Madison quickly got necessary parts ordered and shipped to WAIS Divide.
- Many large pieces of equipment no longer need at WAIS Divide were shipped out on flights of opportunity. Shipments included:
- Pengo cable tensioner
- Spare drill cable
- P05 cable spooler
- Electrical equipment spares
- Components that can be used on the Intermediate Depth Drill
- Heavy Equipment Support
- Excellent support by operators
- Equipment held up well and needed few repairs
- Excellent maintenance of Arch doorways during inclement weather
- Generators
- The power system was reliable and had only a few unscheduled outages including the failure of the main breaker on December 12.
- The generator that failed last season was not available until December 19 because the repair parts originally ordered were not the right ones. An emergency back-up, however, was in place.
- Switch gear was not operational and all equipment had to be shut down for the generators to be switched. This was not, however, a big problem.
IDDO Goals for the Season:
- "Dial-in" replicate coring system
- Collect at least 252 meters of high quality replicate core from five requested depths
- Improve methods of broaching, milling, and coring off the parent borehole
Drilling:
REPLICATE CORING A HUGE SUCCESS - first replicate core successfully collected December 17, 2012 and replicate core collected from all intervals of interest. IDDO believes that these are the first ever cores taken from deviations from the high side of the borehole either in ice or rock. The tremendous success of the replicate coring at WAIS Divide is the result of the ingenuity and hard work of the DISC Replicate Coring Development Project team headed by Alex Shturmakov and the WAIS Divide Project drill crew, especially Jay Johnson, Nicolai Mortensen, and Chris Gibson who were members of both teams.
- All five deviations were completed with coring intervals between 1952 and 3100 meters. Drilling progress is shown in the following graph.
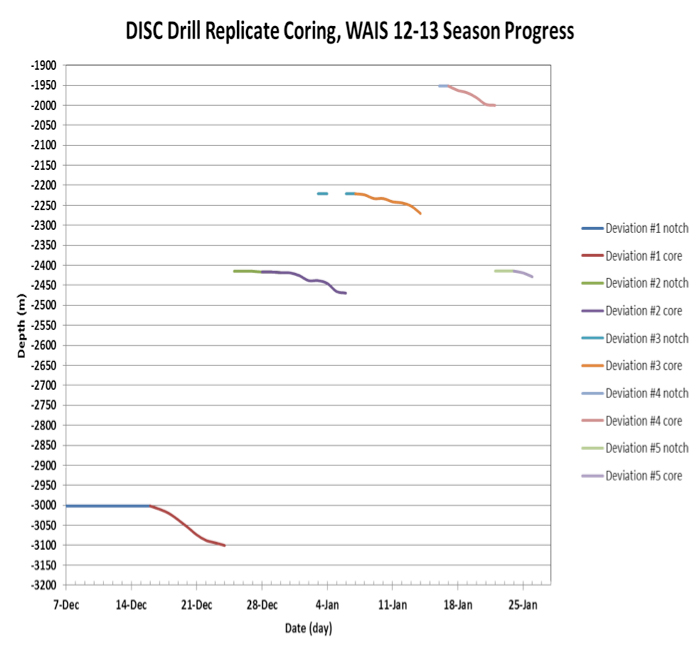
- Total core drilled: 285.4 meters
- Replicate core had good depth-age correlation to the main core, as witnessed by ash layer depth matching.
- Tripping speeds
- Descended at up to 1 m/s with pump running
- Ascended at up to 2.3 m/s
- Cutter speed
- 60 to 110 rpm for broaching and milling
- 80 rpm for coring
- Coring penetration rates of 3 to 4 mm/s
- Borehole fluid density
- Density maintained at 0.920 @ -31°C throughout the season
- Fluid mixed to density of 0.935 @ -31°C to compensate for 141b losses
- 12,398 liters (3,275 gal) of fluid used
- 7,823 liters (2,067 gal) of Isopar K
- 4,575 liters (1,209 gal) of 141b
- Total fluid loss for season was 104% compared with
- 2011-12 season loss of 91%
- 2010-11 season loss of 43%
- 2009-10 season loss of 25%
- 2008-09 season loss of 37%
- 2007-08 season loss of 35%
- Losses for this season and the 2011-12 season are estimated because the exact volume of each deviation notch is not known. Estimated loss is higher than in past seasons due the replicate coring.
- Total of 71 days at WAIS
- 12 days for arch work and set-up
- 3 days for testing
- 53 days for replicate coring operations
- 3 days for packing at end of season
Challenges:
- Winch clutch - bearing in clutch started to make noise indicating start of potential failure
- Small winch motor - motor at times would not stop on command. This problem was first experienced last season. The e-stop had to be used to stop the motor.
- Crown sheave - 3 of 6 screws that mount the hub to the sheave sheared; all screws replaced.
- Frost build-up in the magnetic coupler of pump
- Caused high running current or prevented the pump from starting
- Problem mitigated by preventing ice particles from entering the housing
- Preventing the broaching head from cutting while ascending
- The "bumper" designed to prevent the problem did not work well when hole inclination was more than a few degrees.
- A new "drop ring" was designed and implemented in the field. Implementation was in stages to reduce impact on drilling.
- Catching the casing with the broaching head. Care had to be taken when raising the broaching head through the casing to prevent head from catching the casing and shaving pieces off the casing.
- Failure of shear pins in the actuator arms - some drilling scenarios require care to prevent failure.
- Icing in the actuator arm ball nut - required that maintenance be performed routinely
- Instability of control software - frequent , random crashing of software
- Level wind encoder failure - had to be replaced with spare
- Axial stick-slip made creating initial ledge with milling head very time consuming - broaching cutters were added between the milling cutters to improve efficiency of cutting process
- Collecting chips from the broaching process
- Majority of cuttings were left in borehole and were collected later on coring runs
- Check valve design was changed to improve chip collection
- Chips from the lower two deviations settled to the bottom. Recovery attempts at the end of the season proved to be very time consuming and dangerous - risk of getting drill stuck - due to the warm borehole temperature and the chips re-sintering together.
- Broaching chips clogged pump on several occasions.
- Compressed air used to clean pump before each run
- Led to failure of motor driver
- Cutter head problems:
- Screw failure, probably due to screw failure itself and poor cutter fit, caused the loss of two cutters and hardware down hole
- The conical tool was used to recover all parts after magnet tools fabricated onsite failed to retrieve the parts
- All cutters were modified to improve fit and accept different screw type
- Instrument section problems were ongoing
- Motor Drivers failed due to presence of larger-than-usual chips from broaching (Locked rotor)
- A logic level incompatibility showed itself at low temperatures intermittently on an internal serial bus causing lock-up of the bus
- Leaks continue to be an issue
Borehole Camera:
- Excellent downhole videos were obtained this year using a re-designed borehole camera
- New features of the borehole camera include
- Forward light head that greatly improved image quality over "ring" lighting used in previous design
- Internal battery pack, which, along with internal data storage greatly simplified the camera
- Internal data storage; data downloaded via external USB port
- Mounts in core barrel
Logging Tool Test:
- The ability to move a logging tool past deviations was an important requirement for the replicate coring system and operation.
- To test the implementation of this requirement, a 30 lb dummy logging tool that mimicked Gary Clow's temperature logger was lowered through each of the deviation zones.
- Tool was suspended below the borehole camera by a 10 m tether.
- Weight on bit was monitored to verify that the tool did not get hung up at the deviations.
Lessons Learned:
- Overall System
- The testing and upgrades done since last season were a major factor in the success of this season
- The ability to configure the drill barrels to a desired length was very important and useful
- The course alignment procedure is needed for the drill to repeatedly reach its desired inclination
- An entire deviation can be done with the actuators clocked in the opposing configuration
- Control system/electronics
- The sonde and winch control programs need work; they don't run reliably and must be restarted frequently
- Auto azimuth works well
- No matter how much testing is done off season, you will always have new surprises in the field
- Cutter heads
- The new broaching cutters worked well, especially with rotation
- The new milling head worked much better
- Once an initial ledge was formed, milling with shoes worked very well
- The coring head cutters must have a tight fit with the pocket in the head
- A conical tool is very effective in aiding the recovery of metal objects at the bottom of a borehole
- Surface operations
- The new barrel wrenches worked much better
- Rigidly mounting the transit to the core transfer truss simplified the alignment procedure
- Machine Shop
- Critical to the success of this season
Safety:
Overall the 2012-13 season was very safe.
- Air Monitoring
- Ventilation system worked well again this season
- Approximately 1-2 air monitor alarms per drill run
- Alarmed mainly during ascent tripping
- O2 sensor still will not hold calibration
- Trouble keeping screen cleaning sample line frost free
- Tried to get handheld O2 monitor ordered from McMurdo, but it had not arrived by the end of the season
- NICL monitor maintained by Don Voigt/SCO
- Ventilation system worked well again this season
- Only two reported injuries this season
- One sustained in McMurdo - Shoulder injury led to subsequent NPQ, return to NZ for MRI and re-PQ. IDDO believes that the McMurdo medical personnel overreacted to the person's injury in sending them back to NZ for MRI.
- One sustained during packing at the end of the season - Cheek injury just below eye when hit by Amphenol connector while coiling stiff cables
End of Season:
- Began packing the drill, January 28-30 - Good headway was made on next season's work
- Debriefing held at WAIS Divide January 27
- Remaining nine drillers left WAIS Divide on February 1